5月12日,由陜西化建承建的福建中景石化有限公司全球最大單套年產100萬噸丙烷脫氫項目在福清江陰鎮正式投產,產品聚合級丙烯各項技術參數和性能均滿足工藝專利商和設計的各項技術指標要求,這標志著中景石化二期丙烷脫氫裝置順利達產。陜建集團黨委委員、副總經理、陜西化建黨委書記、董事長高建成出席項目投產儀式并致辭、剪彩。
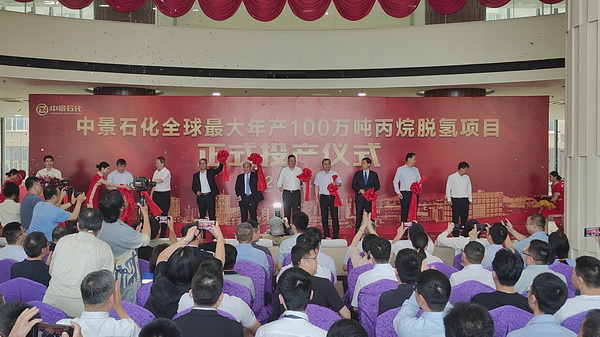
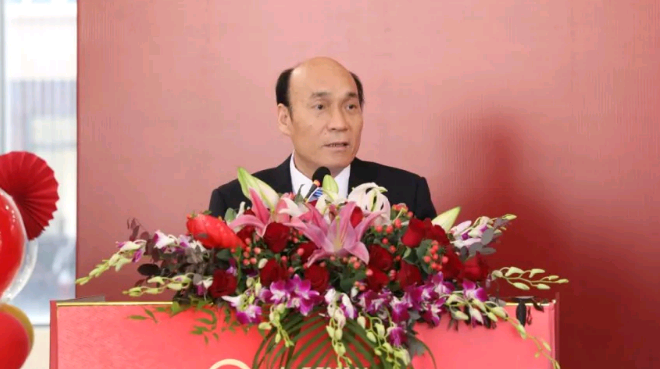
高建成致辭中表示,陜西化建和中景石化集團有著長期、良好的戰略合作關系,先后承建了中景石化120萬噸/年聚丙烯項目、美得石化100萬噸/年丙烷脫氫項目、萬景石化100萬噸/年丙烷脫氫等項目,雙方建立了深厚的友誼,實現了共贏發展。陜西化建將始終秉承“以質量求生存、以信譽求發展”的宗旨,一如既往、全力以赴為福建中景集團后續項目建設提供高標準、高質量的服務,努力為中景石化集團打造全球最大的丙烷脫氫生產基地、實現高質量發展貢獻陜西化建的力量。
該項目引進美國魯瑪斯公司世界最先進的丙烷脫氫制丙烯技術和專利,在技術引進、工程設計、設備制造、土建工程、設備安裝等方面,堅持科技引領、創新驅動,研制了反應器特閥、產品氣壓縮機、50MW正壓防爆電機、169MW空氣加熱爐、軸流泵等核心設備,在行業內首次實現設備及配件國產化率超99.5%,打破了國外技術壟斷,創造了全球、全國十幾個首臺套設備,為中國企業智造化工設備走向全球打下堅實基礎。
江陰港城經濟區管委會副主任邱華焰、中景石化集團董事局主席翁聲錦、美國魯瑪斯技術公司大中華區總經理王皓、科萊恩化工科技(上海)有限公司亞太區生產運營總監沙杰睿及相關工程設計方、設備制造方和監理等單位代表出席。
當天,中景石化舉行了“中景石化全球最大年產100萬噸丙烷脫氫項目正式投產慶典暨2024年度全球客戶大會”,陜西化建因在年產100萬噸丙烷脫氫項目及120萬噸聚丙烯項目建設過程中出色的專業施工能力和敢打硬仗的鐵軍作風,榮獲中景石化集團唯一的特別貢獻獎。
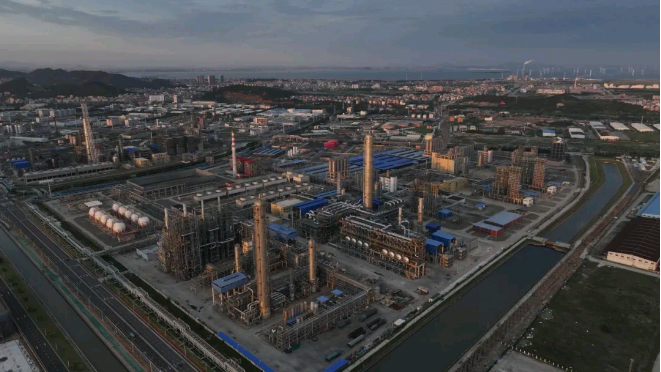
該項目于2022年3月開工建設,公司調配優秀的管理團隊,投入充足的生產要素。廣大參戰職工精誠團結、齊心協力,精心組織,科學管理,勇于創新,先后克服了梅雨施工、交叉作業等諸多困難,在產品氣壓縮機、特閥等全場設備及配件國產化率超99.5%的前提下,先后攻克了多項技術難題,屢創佳績,圓滿完成施工任務。
本項目采用單塔分離設計,高度達138米的丙烷丙烯分離塔是中景石化年產100萬噸丙烷脫氫項目最核心設備,也是全球高度最高、容積最大的丙烷丙烯分離塔,重量為2700噸、容積達11000立方米。項目團隊結合現場實際,采用“地面穿衣、分段吊裝、空中組對”的工藝進行安裝,從2022年10月2日丙烷丙烯分離塔的第一段就位開始,克服了高空強風對吊裝、組對、焊接等不利因素,于11月20日提前8天圓滿完成丙烷丙烯分離塔封頭與塔身在百米高空完成絕美“合體”,標志著全球高度最高、容積最大的丙烷丙烯分離塔吊裝工作圓滿完成,用實際行動彰顯陜西化建“硬實力”。
提前45天完成裝置的動力“心臟”——國內首臺套最大的產品壓縮機安裝。該項目采用國內首臺套最大的多段離心式壓縮機,長寬高為27米×6.5米×5.0米,總重達937噸,且機組進、出口管線直徑達到2.4米、2.0米、1.5米等超大規格,管理團隊經過多方論證,優化國內最大產品氣壓縮機進出口管線上的膨脹節、異徑管安裝位置,采用“順序安裝、循環找正、逐一固定”的安裝方法,精準找正機組、無應力配管。實現了國內首臺套最大50MW大功率電驅的多段產品氣離心式壓縮機一次性開車成功,且機組振動值遠低于制造設計要求,刷新了國內大型壓縮機安裝紀錄。
深入研究圖紙,精準領會設計意圖,圓滿完成了裝置高溫核心反應區設備及工藝管道安裝、調試任務,為解決工藝管道的精準安裝,經過反復研究,確定采用以設計最大熱膨脹量的高溫管系為基準,綜合反應器整體五條大口徑管系進行同軸度調整、預制安裝,滿足了反應器整體高溫管系熱態運行下位移、應力要求。同時,在結合LUMMUS和支吊架制造廠家要求的基礎上,經分析研判,確定以八臺反應器高溫管線四向限位點為基準進行彈簧支吊架的安裝、調整,實現了反應器高溫群管線支吊架冷態調整最短周期內一次性通過。
丙烷脫氫反應器是裝置的核心設備,規格為臥式Φ7900mm×20204mm,單臺重300多噸,結構形式為大直徑薄壁雙層結構容器,局部設計有高鉻鎳不銹鋼襯里,現場吊裝就位難度極大。為確保反應器吊裝工作順利進行,項目班組多次討論,勘測現場,優化方案,編排吊裝計劃,妥善解決道路運輸受限、場地空間狹小及設備“體積大、吊裝難”等諸多不利因素,通過調整優化反應器空中翻轉力矩,采用“平衡梁--單滑車--雙吊機”工藝,實現反應器仙人掌的地面組裝,節約了仙人掌空中組對的施工成本和工期。在2個月時間內實現了所有反應器“安全、有序、高效”吊裝就位,有力保障了工程進度,在大重型設備吊裝空中翻轉等方面積累了經驗。該大型臥式反應器空中翻轉等技術獲得了陜西省化工學會科技成果二等獎、中國化工施工企業協會部級工法等榮譽。
丙烷脫氫(PDH)裝置的高溫循環管的焊接和安裝是施工一大難點,管道材質為TP321H不銹鋼和鉻鉬合金鋼,管道口徑和壁厚大、焊接難度大。加之,管線運行過程頻繁加載的溫度及工藝管線的走向,對TP321H高溫管道的焊縫及支吊架安裝提出了更高的要求,公司技術中心組織人員研究圖紙、技術要點,多次召開專題會進行論證,決定對大口徑管道定位、組對采用“五線五測五同軸”技術對8臺反應器的三通進行定位,以確保三通的中心在同一水平線。有效解決了大管道焊接慢、施工難、質量難以控制的難題。同時通過采用“實芯焊絲管道固定口全位置自動氬弧焊技術”,解決了直徑DN2700的大口徑TP321H管道焊接難題,一次合格率達到99.5%以上、提高了焊縫質量,起到了降本增質增效的目的。
針對反應器下方24臺最大單重達20噸的特閥安裝,通過自行研發制造了“大口徑管道組成件運輸頂升安裝工裝”,有效解決了狹小空間大型特閥的運輸、安裝就位的技術難題。對于特閥執行機構高壓液壓系統調試過程中的振動過大的問題,通過采用重型管卡,優化了系統的管道支架,減少對液壓系統振動造成的疲勞損傷,降低系統的安全隱患。
項目團隊通過精心組織、科學管理,克服疫情、梅雨季節等各種不利因素的影響,攻克多種技術難題,達到了本裝置調試最短,運行最佳的效果,得到了工藝包供應商LUMMUS及建設單位、設計單位的高度評價,認為施工技術水平處于國內領先水平。
在中景美得石化PDH2 100萬噸/年丙烷脫氫項目正式投產之際,由陜西化建承建的另外一套中景石化PDH3 100萬噸/年丙烷脫氫項目亦在緊張有序的施工當中,預計今年9月將建成中交。
據悉,中景石化是目前全球唯一擁有從液化石油氣碼頭、低溫罐區、丙烷制造、丙烯制造、聚丙烯制造到制成聚丙烯薄膜等新材料的全產業鏈企業,享有“世界膜王”的美譽。項目全部投產后,中景石化將成為全球最大的丙烯、聚丙烯生產基地。本次投產的100萬噸丙烷脫氫項目總投資40億元,年產值可達100億元,可拉動下游產業鏈產值200億元,是目前全球最大的丙烷脫氫制丙烯單套裝置。(卂杢 何政正)